Understanding the Role of MES Platforms in Lean Manufacturing
One of the key strategies for achieving this is adopting lean manufacturing principles, which focus on eliminating waste and maximizing value. In this context, Manufacturing Execution Systems (MES) platforms play a crucial role in enabling and supporting lean practices within manufacturing facilities.
MES platforms serve as the backbone of modern manufacturing operations, providing real-time visibility and control over production processes. By integrating MES into their operations, manufacturers can streamline workflows, minimize downtime, and reduce inefficiencies. MES platforms collect data from various sources across the production floor, including machines, sensors, and operators, and provide actionable insights that help identify areas for improvement.
It facilitates the implementation of lean manufacturing principles by enabling better resource allocation and utilization. With features such as production scheduling, inventory management, and quality control, MES platforms help manufacturers optimize their resources and minimize waste. By providing accurate and timely information, MES platforms empower decision-makers to identify bottlenecks, address issues proactively, and continuously improve processes. Overall, MES platforms play a critical role in driving lean transformation within manufacturing organizations, enabling them to achieve greater efficiency, productivity, and competitiveness.
Upgrade Production Processes with MES Platforms
Manufacturing Execution Systems (MES) platforms offer a comprehensive suite of tools and functionalities designed to streamline production processes and enhance operational efficiency. These platforms act as centralized hubs for managing and monitoring all aspects of manufacturing operations, from production scheduling to quality control. By leveraging MES platforms, manufacturers can automate manual tasks, standardize processes, and eliminate unnecessary steps, resulting in smoother and more efficient production workflows.
One of the key features of MES platforms is their ability to provide real-time visibility into production activities. By collecting data from various sources across the factory floor, including machines, sensors, and human operators, MES platforms enable operators and managers to monitor production progress, track key performance indicators (KPIs), and identify potential issues in real-time. This real-time visibility allows manufacturers to make data-driven decisions, optimize resource allocation, and respond quickly to changing production demands
MES platforms facilitate collaboration and communication among different departments and stakeholders involved in the production process. With features such as centralized dashboards, alerts, and notifications, MES platforms ensure that everyone has access to up-to-date information and can communicate effectively across the organization. This enhanced communication and collaboration help reduce errors, improve decision-making, and foster a culture of continuous improvement within the manufacturing facility. Overall, MES platforms play a crucial role in upgrading production processes, increasing operational efficiency, and driving business growth.
Enhancing Productivity Through MES Optimization Strategies
Manufacturing Execution Systems (MES) are powerful tools that can significantly enhance productivity in manufacturing operations when optimized effectively. Implementing MES optimization strategies involves leveraging the full capabilities of MES platforms to streamline processes, improve efficiency, and maximize output. By focusing on key areas such as automation, data analytics, and integration, manufacturers can unlock new levels of productivity and competitiveness.
One of the primary strategies for optimizing MES is automation. MES platforms offer a wide range of automation capabilities, including automated data collection, scheduling, and reporting. By automating repetitive tasks and workflows, manufacturers can reduce manual intervention, minimize errors, and increase throughput. Additionally, automation enables real-time monitoring and control of production processes, allowing for faster response times to issues and better resource utilization.
Another important aspect of MES optimization is data analytics. MES platforms collect vast amounts of data from various sources throughout the manufacturing process. By leveraging advanced analytics tools, manufacturers can gain valuable insights from this data to identify trends, detect anomalies, and optimize performance. Analytics-driven decision-making enables manufacturers to make more informed choices, improve predictive maintenance strategies, and optimize production schedules for maximum efficiency.
Integration is also critical for MES optimization. Integrating MES platforms with other systems such as Enterprise Resource Planning (ERP) and Customer Relationship Management (CRM) systems allows for seamless data exchange and process synchronization across the organization. This integration eliminates silos, improves communication, and ensures that all departments have access to accurate, up-to-date information. By breaking down barriers between different systems and departments, manufacturers can streamline operations, reduce inefficiencies, and drive productivity gains.
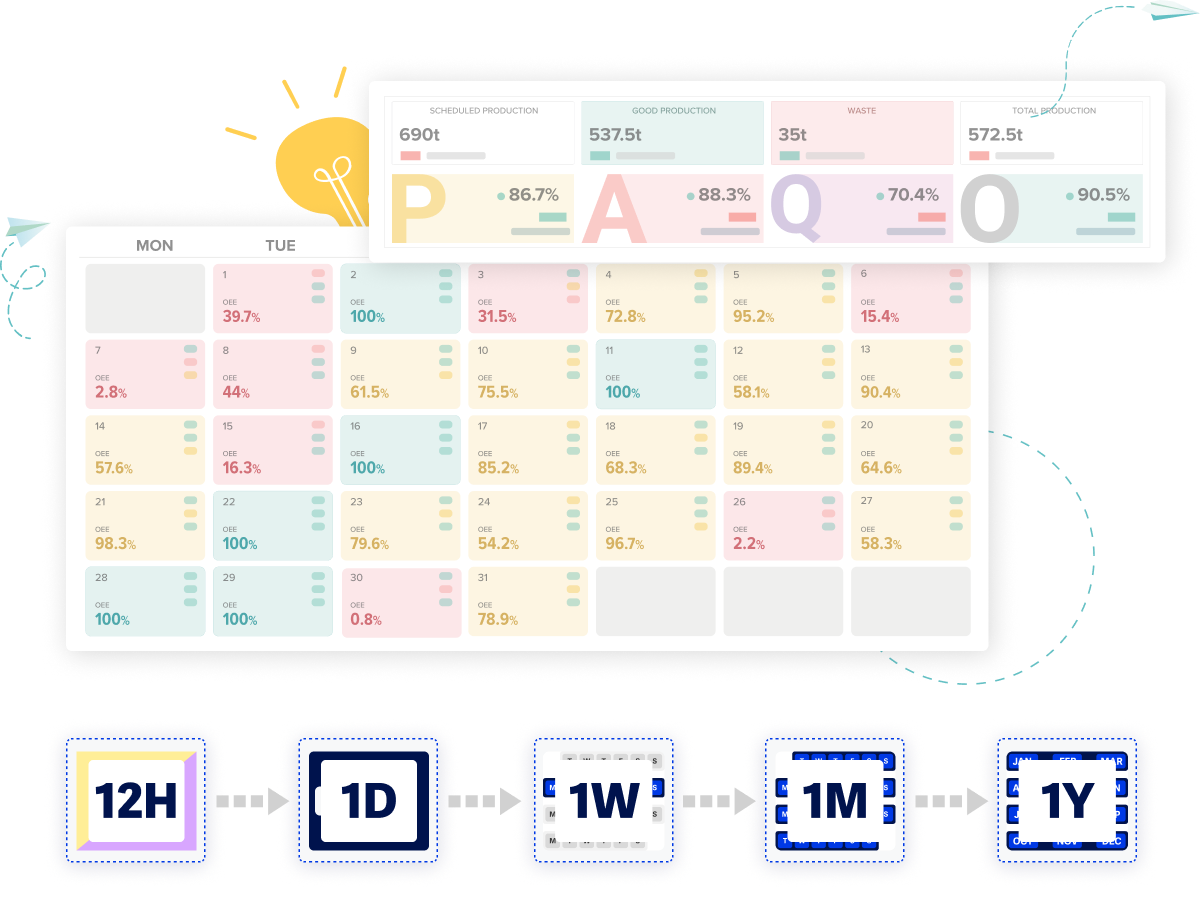
See your production summary of anytime with MES Software
Harnessing MES Data for Continuous Improvement
Manufacturing Execution Systems (MES) generate vast amounts of data that can provide valuable insights for continuous improvement initiatives. By harnessing MES data effectively, manufacturers can identify inefficiencies, optimize processes, and drive ongoing improvements in productivity and quality.
The first step in harnessing MES data for continuous improvement is to establish clear performance metrics and key performance indicators (KPIs). These metrics should align with business objectives and provide a clear picture of performance across different aspects of manufacturing operations, such as production output, downtime, and quality metrics. By defining these metrics upfront, manufacturers can track progress and identify areas for improvement more effectively.
Once performance metrics are established, manufacturers can leverage MES data analytics tools to analyze the data and identify trends, patterns, and root causes of inefficiencies. Advanced analytics techniques, such as machine learning and predictive analytics, can help manufacturers uncover hidden insights and anticipate potential issues before they occur. By analyzing MES data in real-time, manufacturers can make data-driven decisions to optimize processes, minimize downtime, and improve overall efficiency.
Manufacturers can use MES data to implement continuous improvement initiatives such as lean manufacturing practices and Six Sigma methodologies. By identifying areas of waste, bottlenecks, and variability in production processes, manufacturers can develop targeted improvement projects to streamline operations and eliminate inefficiencies. MES data provides the foundation for these initiatives, enabling manufacturers to track progress, measure the impact of improvement efforts, and drive sustainable improvements over time.
Achieving Lean Manufacturing Excellence with MES Platforms
Lean manufacturing principles focus on eliminating waste, improving efficiency, and optimizing processes to create value for customers while minimizing costs. MES platforms play a crucial role in supporting lean manufacturing initiatives by providing real-time visibility, data-driven insights, and automation capabilities that enable organizations to streamline operations and drive continuous improvement
One of the key features of MES platforms is their ability to provide real-time visibility into production processes. By capturing data from shop floor equipment and integrating with other systems such as ERP and CRM, MES platforms enable manufacturers to monitor production in real-time, identify bottlenecks, and respond quickly to changing demand. This real-time visibility allows organizations to optimize production schedules, minimize downtime, and ensure that resources are utilized efficiently.
In addition to real-time visibility, MES platforms also offer powerful analytics capabilities that enable organizations to analyze production data and identify areas for improvement. By leveraging data analytics tools, manufacturers can identify trends, patterns, and root causes of inefficiencies, allowing them to implement targeted improvement initiatives that drive operational excellence. Whether it's reducing cycle times, improving quality, or minimizing waste, MES platforms provide the data-driven insights needed to achieve lean manufacturing goals.
MES platforms enable organizations to automate manual processes, reducing the risk of human error and improving overall efficiency. By automating tasks such as data collection, reporting, and workflow management, manufacturers can streamline operations, reduce lead times, and increase throughput. This automation not only improves productivity but also frees up resources to focus on value-added activities, such as process optimization and continuous improvement.
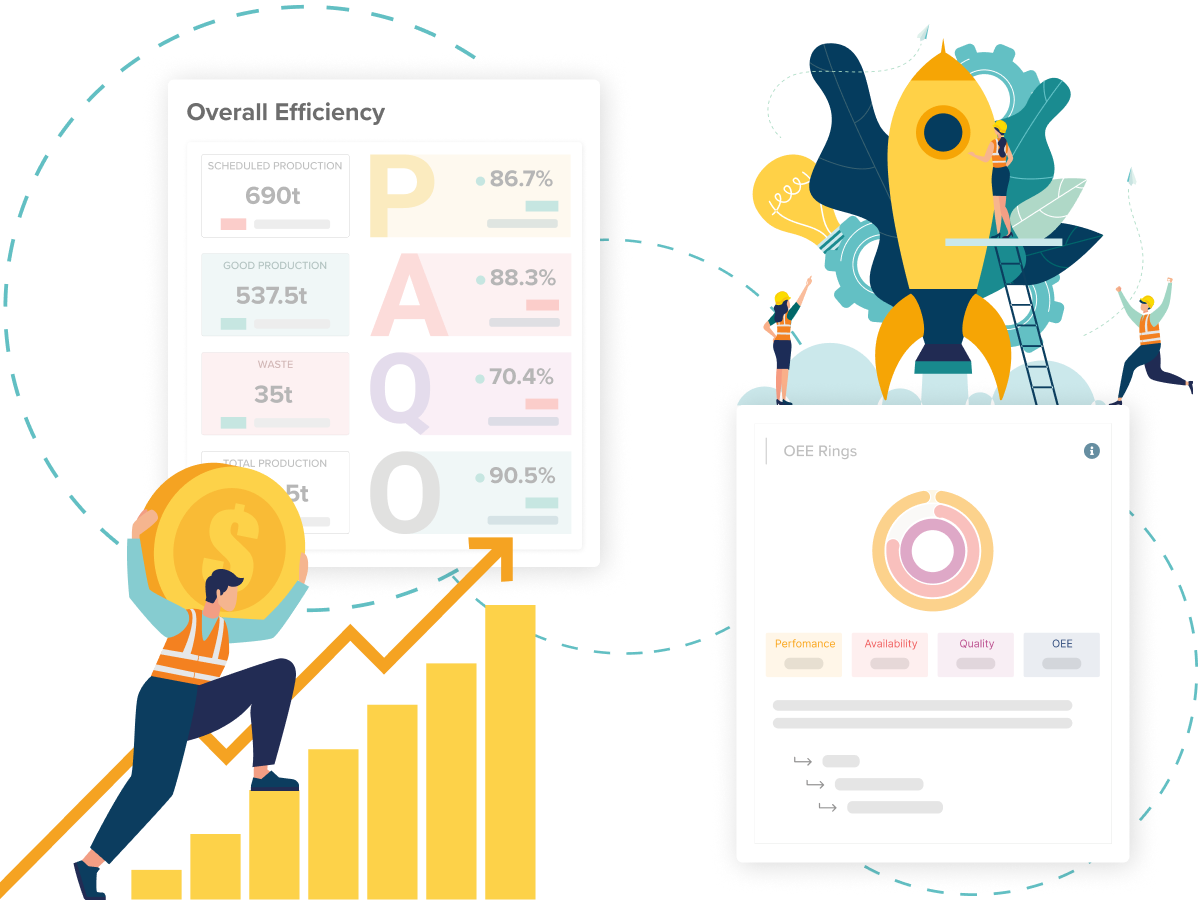
Increase Production Efficiency
Conclusion
MES platforms are indispensable tools for modern manufacturing operations seeking to optimize their processes, drive efficiency, and achieve lean manufacturing excellence. By harnessing the power of real-time visibility, data analytics, and automation, MES platforms empower organizations to identify inefficiencies, streamline operations, and drive continuous improvement initiatives. Through the adoption of MES technology, manufacturers can enhance productivity, minimize waste, and respond effectively to changing market demands. With MES platforms at the forefront of their operations, companies can unlock new levels of efficiency, agility, and competitiveness, ensuring their readiness for the challenges and opportunities of the future manufacturing landscape.